Utilizing the latest technology, we specialize in fabricating durable, long-lasting plastic dip tanks from top-grade plastics for the commercial and industrial sector to withstand the demands of rugged service.
We employ rigorous spark and hydro tests before shipping to ensure the quality and safety of our dip tanks. Our team of experts collaborates with you, considering your plant location, space, capacity, and process requirements to design an optimal tank system that best meets your industry needs.
Hydro dipping tanks in the industrial plastics industry serve a vital role in transferring intricate designs and patterns onto three-dimensional plastic components. This process, also known as water transfer printing, involves floating a film with a desired pattern on water, then immersing the plastic part, allowing the design to adhere. The process yields highly detailed and custom finishes on products, enhancing their aesthetic appeal.
There are various dip tanks in total, each serving a specific purpose in the industry.
Types of Dip Tanks
Hydro Dipping Tanks
- Hydro dip tanks (also known as hydrographic dipping tanks, water transfer printing tanks or immersion printing tanks) play a significant role in adding detailed and intricate designs to plastic parts and facilitate the transfer of intricate designs onto plastic components. Through a water immersion process, desired patterns from specialized films adhere to objects, offering customization and enhanced aesthetics for a variety of products.
Paint Dipping Tanks
- Paint dip tanks enable the application of uniform paint layers on plastic components. These tanks use immersion techniques to ensure consistent coloring and finishing, enhancing product aesthetics and quality.
Screen Dipping Tanks
- Screen dip tanks are used for cleaning and reclaiming silk screens. By immersing screens in these tanks, residues of ink and emulsion are removed, ensuring screens are pristine for subsequent printing processes on plastic components.
Chemical Dipping Tanks
- Chemical dip tanks are used for treating plastic components with specific chemicals. This immersion process can clean, etch, or modify surfaces, preparing them for painting, bonding, or other manufacturing stages, thus ensuring quality control and consistent finishing.
Wax Dipping Tanks
- Wax dip tanks facilitate the application of protective wax coatings on plastic parts, aiding in mold release, improving surface finishes, and ensuring consistent product quality during manufacturing.
Acetone Dipping Tanks
- Acetone dip tanks are employed for cleaning and surface preparation. By immersing plastic parts, they efficiently remove residues, smooth surfaces, and enhance adhesion properties, ensuring optimal finish and bonding during subsequent processes.
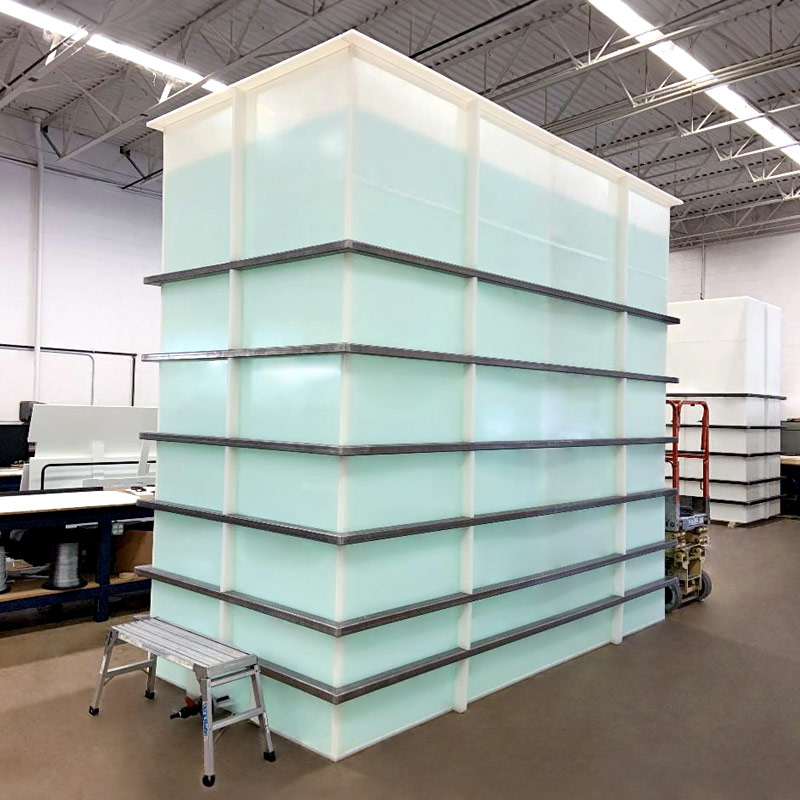